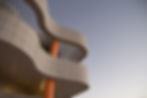
The Ultimate Guide to Six Sigma: Everything You Need to Know In 2025
0
20
0
TL;DR
Six Sigma is a data-driven methodology aimed at reducing defects and optimizing processes.
It is structured around two key frameworks DMAIC and DMADV
Statistical analysis and structured project management are core to its success.
Belt-based certifications (White, Yellow, Green, Black, Master Black) guide professional development.
Six Sigma is applicable across diverse industries from manufacturing and healthcare to IT and finance.
Organizations use it to improve efficiency, reduce operational costs, and enhance customer satisfaction.
What is Six Sigma?
Six Sigma is a data-driven methodology developed to eliminate defects and improve the quality of business processes. Originally introduced by Motorola in the 1980s, and later championed by General Electric in mid 1990's. Six Sigma has evolved into a global benchmark for operational excellence.
The approach relies heavily on statistical tools and quality management methods to identify root causes of inefficiencies and drive sustained improvement.
Whether you're improving a manufacturing process or optimizing a digital workflow, Six Sigma provides the structure and discipline to deliver consistent, high-quality results.
Why Six Sigma Matters Today
In an increasingly competitive and digitized business landscape organizations must ensure their processes are both efficient and adaptable.
Six Sigma offers a framework that not only reduces variability but also aligns business operations with customer expectations.
Companies today are dealing with rapidly changing technology, customer preferences, and economic fluctuations.
Six Sigma helps leaders make decisions backed by data and not assumptions, improving everything from supply chain operations to customer service delivery.
It is especially critical in industries where quality and precision directly affect safety, profitability, or brand reputation.
Core Principles of Six Sigma
Six Sigma is grounded in a few fundamental principles that guide its successful implementation.
First, it puts the customer at the center of every decision, ensuring that improvements translate into real value.
Second, it emphasizes understanding and mapping existing processes to identify inefficiencies.
Third, it aims to reduce variability and remove steps that do not add value. Additionally, Six Sigma empowers employees with the right tools and training, promoting a culture of continuous improvement.
Finally, it advocates a structured approach to problem-solving using proven methodologies like DMAIC or DMADV.
Six Sigma Methodologies: DMAIC vs DMADV
Six Sigma utilizes two main methodologies depending on whether you're improving an existing process or building a new one.

DMAIC, which stands for Define, Measure, Analyze, Improve, and Control, is used to refine existing processes. It begins with clearly defining the problem, measuring performance, analyzing data, implementing improvements, and putting controls in place to sustain results.
On the other hand,
DMADV - Define, Measure, Analyze, Design, and Verify is used for developing new products or services where no existing benchmark exists. Both methods are systematic, data-driven, and rooted in customer-focused outcomes.
Real-World Process Improvement Examples
Six Sigma is not just theoretical in the real world business scenarios. It has helped 1000s of businesses from global Enterprise to startups save millions and improve operations.
For example,
A hospital might use Six Sigma to reduce patient waiting times improving both operational efficiency and patient satisfaction.
A manufacturing firm might cut down on defects in production lines, leading to reduced costs and improved product quality.
Service industries like banking and insurance have applied Six Sigma to enhance transaction accuracy and speed up processing times.
These examples show that Six Sigma is flexible and can be adapted to any industry looking to optimize performance.
Key Six Sigma Metrics
Measuring performance is one core aspect of Six Sigma. Metrics provide objective insight into the health of a process and the effectiveness of improvements.
Some of the key metrics include
Defects Per Million Opportunities (DPMO), which measure how often a process fails. Sigma Level, which indicates the performance quality of a process
Cycle Time, which tracks how long it takes to complete a process from start to finish.
Understanding and monitoring these metrics enables businesses to set benchmarks, identify outliers, and continuously improve toward operational excellence.
Tools Used in Six Sigma:
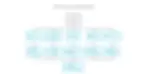
Histograms – Bar charts that show how data is distributed.
Cause-and-Effect Diagrams (Fishbone) – A way of figuring out all possible reasons for a problem.
Check Sheets – Simple forms to track how often specific issues occur.
Control Charts – Used to monitor how consistent a process is over time.
Flowcharts – Diagrams that show every step of a process, helping to spot flaws.
Another popular tool is the “5 Whys” Technique, where you keep asking “why?” to dig deeper into the root cause of a problem. For larger scale improvements practices like Process Mapping and creating a Project Charter are commonly used to visualize workflows and set clear goals.
Six Sigma Certification Levels
Six Sigma certifications are categorized by 'belts' similar to martial arts.
A White Belt offers a high-level overview of Six Sigma principles.
Yellow Belts support project teams by understanding the basics and assisting in data collection.
Green Belts lead smaller projects and often work part-time on Six Sigma initiatives.
Black Belts are full-time professionals who lead projects, mentor Green Belts, and drive strategic change.
Master Black Belts are experts who provide enterprise-level oversight and training.
Each belt builds upon the previous, offering a clear progression for professionals aiming to grow in process improvement roles.
How to Get Six Sigma Certified
Getting certified in Six Sigma starts with choosing the right belt level based on your career goals and experience. These programs typically include online or in-person training, real-world project simulations, and exams.
After training, you’ll complete a certification exam that tests your understanding of Six Sigma tools, principles, and problem-solving techniques. Finally, applying your skills in actual projects helps reinforce your knowledge and demonstrates your capability to employers.
You can explore SigmaForces' specialized training programs, which provide certifications to accelerate your professional growth.
Is Six Sigma Certification Worth It in 2025?
With the growing importance of operational excellence and data-driven decision-making, Six Sigma certification continues to offer significant value in 2025.
Professionals with Six Sigma credentials are highly sought after across industries for their ability to drive efficiencies, lower costs, and improve quality.
Beyond job opportunities, certification can also lead to career advancement, higher salaries, and leadership roles in process improvement initiatives. Whether you’re entering the job market or looking to transition into a new role, Six Sigma adds a powerful edge to your resume.
Six Sigma vs Other Methodologies
Six Sigma isn’t the only approach to process improvement but it stands out due to its strong analytical foundation.
Lean methodology focuses on eliminating waste and improving flow, while Agile emphasizes flexibility and iterative development, especially in software projects.
Scrum is a framework within Agile used for managing projects through short cycles called sprints.
Each of these approaches has unique strengths, and many companies now use hybrid models, like Lean Six Sigma or Agile Six Sigma, to combine the best of each method.
Choosing the right one depends on your organization’s needs and challenges.
Common Misconceptions About Six Sigma
Despite its proven success, Six Sigma is often misunderstood. One common myth is that it only applies to manufacturing. In reality, it’s been successfully implemented in healthcare, finance, education, and even government.
Another misconception is that Six Sigma is overly complex or math-heavy. While it uses statistical tools, most professionals use software that simplifies these calculations.
Some also believe that Six Sigma is rigid or outdated. On the contrary, its core principles are timeless and adaptable to modern digital transformation efforts.
Six Sigma Success Stories
Many global companies attribute part of their success to Six Sigma. General Electric reportedly saved over $10 billion thanks to its Six Sigma initiatives.
Motorola, where Six Sigma originated, achieved massive improvements in product quality and employee efficiency.
Amazon and Bank of America have also used Six Sigma to refine their customer service and logistics processes.
These success stories highlight how Six Sigma, when implemented correctly, can transform business operations and deliver significant ROI.
Final Thoughts
Six Sigma is more than a set of tools, it’s a culture of excellence. Organizations that adopt its principles can dramatically improve their performance, cut costs, and enhance customer satisfaction.
For professionals, Six Sigma offers a structured career path with global relevance.
Whether you're just starting your Six Sigma journey or looking to deepen your expertise, the methodology empowers you to lead change and deliver measurable results in any industry.
FAQs
Can I learn Six Sigma without a technical background?
Yes. Most programs are designed to teach statistical tools and techniques in an accessible way. No advanced math is required to get started.
How long does certification take?
Is Lean better than Six Sigma?
Are Six Sigma skills relevant in 2025 and beyond?
What industries use Six Sigma?
Can SigmaForces help me get Six Sigma certified?